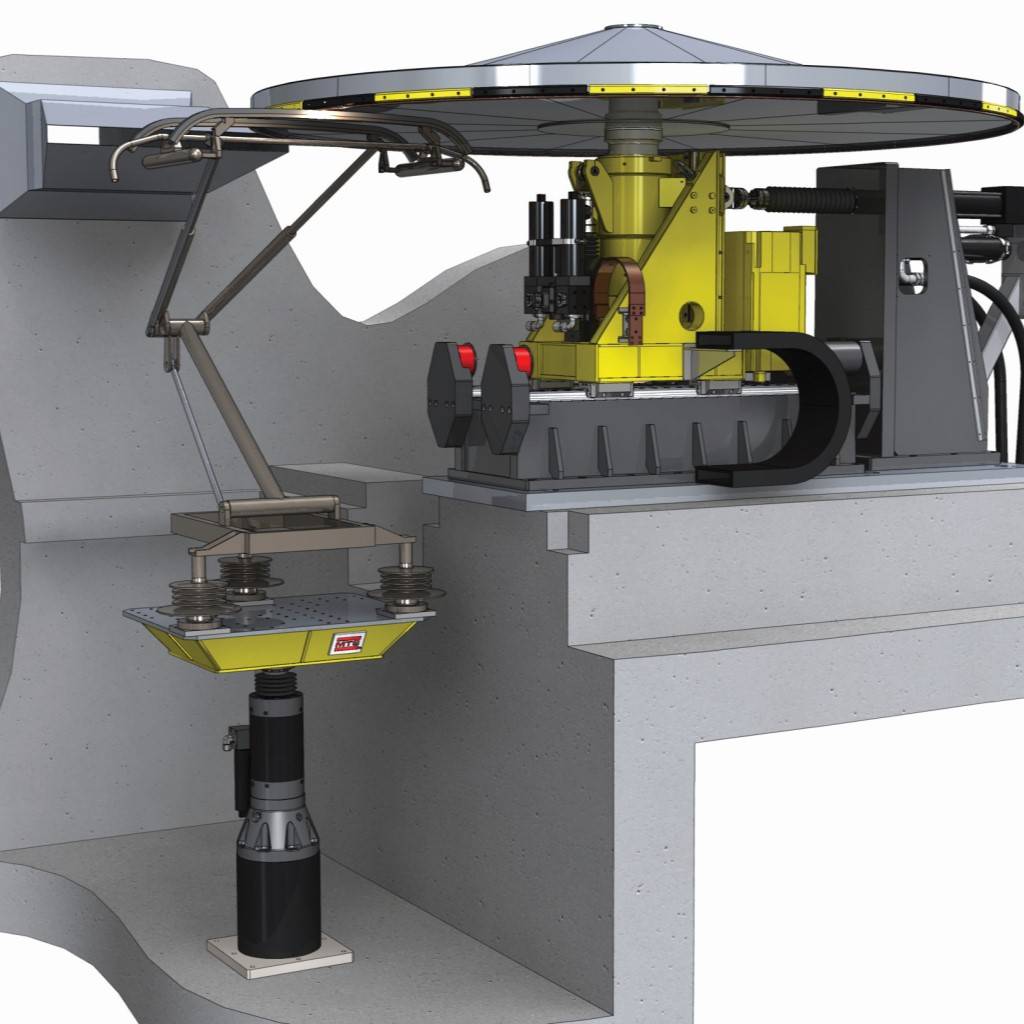
对于列车零部件设计、生产厂家的研究人员和测试工程师来说,电力机车受电弓滑靴与接触网之间的触点构成了一种很复杂也是很有挑战性的环境,其弓网关系尚未充分认知,更不要说进行相应的预测以及产品改进了。
为了确保电力机车的可靠高效运行,受电弓必须与接触网系统上的架空线保持持续接触。然而,这些架空线及其支撑结构在任何给定截面上都呈现出了不同的垂向刚度。接触网系统在 30 m至 100 m间隔内“之”字形布局,以防止受电弓滑靴过度磨损形成切槽。受电弓滑靴与架空线之间的接触力需要维持在合适的范围(70N 至 120N)。如果接触载荷过低,会出现脱网现象,产生电弧放电,不仅会造成机车掉电,还会出现蚀刻和过热现象从而损坏架空线和受电弓滑靴。如果接触载荷过高,由此产生的摩擦会造成架空线和受电弓滑靴的过度磨损。
提供适当的接触载荷需要具有可变的垂向运动能力,但是,当列车的运行速度越来越高,受电弓系统会失去适当的反应能力。即使架空线尽量扁平,也仅当其悬挂支撑不受干扰时才维持接触面扁平。当受电弓抬升架空线时,由此产生的架空线变形会产生波动。如果抬升幅度过大,受电弓会产生更大的波动,导致同一条线路上的下一个受电弓发生接触问题。
解决这些问题对于快速发展的全球高速铁路行业而言至关重要。乘客们需要快速、可靠、舒适的出行服务,但随着铁路机车车辆运营速度越来越快,当前的受电弓技术却成为提升运营速度和服务质量的瓶颈。最坏的情况是,磨损的架空线会出现若干裂缝甚至断裂,进而造成铁路网故障,导致数千趟车次延误甚至取消,而工程人员则要尽快完成维修工作,这一过程成本高、耗时巨大并且效率低下。
复现复杂的弓网交互作用
从测试的角度来看,首要的挑战是如何在可控试验室环境中重建复杂的受电弓动态运营工况。现在,实际投入运营采用轮轨技术的高速铁路车辆已经可以达到最高350 kph (220 mph)的时速,而且新的研发目标正在不断提升最高时速目标。受电弓需要通过非常小的接触区域传递足够高的能量,才能够将重达数百吨的铁路机车加速到期望的最高时速。而正如我们之前所述的那样,受电弓物理部件在滑动环境中与接触网相互作用,纵向运动量大,速度快,承受的载荷持续不断变化。
传统的受电弓研究中,使用了旋转/滑动测试方式,即把架空线安装至直径为1m~2m的转盘上,测试对象是一块碳质材料或者其他材料制品来模拟受电弓滑靴。被测样件推到自旋转盘与架空线接触,并且来回滑动。这样的测试方式可以确定不同材料的磨损效果 ,非常有效,但是它们并不能复现真实系统在实际工况下的动态接触关系。
MTS 系统公司开发的受电弓测试系统提供了更完整的受电弓与接触网动态关系模拟。相应的研发人员和测试工程师能够利用该系统开展受电弓和架空线之间的动力学性能研究,更加契合实际,获取准确的测试结果。该测试系统可以实现弓网的脱网率、接触电阻、功率因数、电弧时间和强度以及滑靴温度的测量测试。此外,还可以针对架空线和受电弓滑靴的磨损和以及轮廓变化进行实时测量。
利用这些测试数据,研发人员和测试工程师可以更好地了解、评估高速铁路受电弓的性能,可以开展接触损耗和相关的影响、接触电阻和电弧放电时长、电弧放电和触点温度以及架空线和受电弓滑靴的磨损影响等方面的研究。最终,测试数据将帮助制造商开发被动式或主动式受电弓悬置系统,提升对架空线运动的动态跟随能力,从而实现更好的接触性能,同时将接触系统的磨损降至很低。
测试系统功能
这套测试系统能够精确复现接触网和受电弓之间的动态交互关系,可以准确模拟各种铁路车辆的运营状态,满足世界各地的测试需求。
该系统将架空线安装在 4m 直径的转盘底部边缘,可以实现模拟最高达 550 kph 的列车运行速度。转盘的旋转运动可以通过编程来模拟真实列车的运营过程。为了能够模拟接触网的垂向位移或刚度,转盘被安装在可以垂向运动的托架之上,也通过编程来复现接触网的垂向位移时间历程或模拟刚度时间历程。转盘托架同样以“之”字形往复运动,以架空线和接触网之间的相互运动。完整的受电弓安装在振动台上,振动台模拟列车在轨道运行时的垂向振动。整个系统可通过受电弓滑靴传输高达 2,000 安培的电流,而高速吹风装置对受电弓滑靴与接触网的接触区域提供冷却,并模拟车辆走行过程中的气动力。测试系统的仪器仪表架跟随架空线进行“之”字形往复运动,对受电弓滑靴和架空线的磨损情况进行实时监测。
整个测试系统的各运动部件具可编程性,能够对受电弓和架空线的实际交互关系进行更加契合真实工况的模拟测试。测试工程师能够借助多种测试模式回放实际的时间历程数据,并调整或者设置不同的测试参数,包括:架空线垂向位移、架空线水平(“之”字形)位移、架空线速度、受电弓垂向运动、受电弓升/降、电流流量和冷却空气流量等。此系统还可提供高度可重复的测试场景,能够对测试物品设计中的微小差异进行详细测量。测试工程师通过这些测量数据,可以更好地了解部件在实际服务环境中的性能和表现,可以信心十足地做出工程决策,优化设计。
在性能参数验证测试过程中,每当修改相应的参数之后,都可以重复实现之前的测试工作。例如,可以对旋转圆盘进行编程使其保持恒定的垂向位置,然后引入越来越大的之字形位移,研究单一参数变化对接触性能的影响。合成数据再现是指根据数字模型预测架空线位移历史记录,并使用先进的数据处理软件,例如MTS的远程参数控制系统软件(RPC®)来实现所需的转盘运动历史记录。
最后,通过实时时间历程回放架空线实测位移量,通过软件再现架空线运动的时间历程,通过改变回放的时间基准,来模拟不同的列车速度,并且可以连接和重复实际运行的短区间数据文件,生成期望总距离(总寿命)的驱动文件。
监测和测量
这套测试系统提高了测试工程师能力,可以实现诸多在“真实世界”中无法实现的测量任务,并以标准化、可重复的方式进行测量。
为了实现这一目标,受电弓测试系统包含了大量先进的监测设备和仪器。其中包括受电弓滑靴与接触网架空线之间的接触载荷和拖动载荷的载荷测量装置。在每根受电弓滑靴的两端包含测量垂向加速度的传感器,可以监测受电弓滑靴对机车和架空线的动态干扰。通过安装在受电弓滑靴背面的传感器和具有记录功能的热成像相机来监测触点温度。激光扫描仪用于检测架空线和受电弓滑靴的外轮廓,用于进行磨损研究。测试系统会自动记录架空线的行程。在受电弓滑靴和接触网的触点输入端和输出端均可进行电流和电压测量,从而可以对接触电阻、功率因数和脱网率进行详细监测。通过光学方法对电弧放电时长和强度进行监测。所有数据均为时间同步采集,以便对特定事件或操作工况进行详细研究。
测试设备的监测渠道也很广泛。其中包括主轴轴承(垂向和水平)加速度以及温度、作动缸载荷和位移、自动润滑系统的工作状态、受电弓升降状态、液压系统和驱动电机系统等等。可以在任意数据采集通道上设置监测限制(包括警告和终止试验),让测试工程师能够精确控制系统安全运行。这些极限检测功能与控制、监测系统相结合,可实现自动测试,无需操作人员持续监测机器。
这些功能可以为受电弓和机车车辆制造商带来巨大的影响。例如,测量运行中的受电弓的接触动力学,包含诸多参数,这些数据对于测试团队来说是具有非常现实的意义。在过去,由于测试系统重复性差,控制能力和精度有限,在试验室获得这样的准确数据堪称天方夜谭。如今,更精确的测试和模拟为获得更具价值的结论奠定了基础。测试工程师可对功率因数和损耗进行更精确的计算,而这两项因素对运营成本有着直接影响。
MTS的高性能受电弓测试系统将引领受电弓测试技术浪潮,这些技术正在改变全球铁路测试团队的研究方式。随着列车运行速度的加快,铁路线路扩展到更多的地区,以及全球乘客数量的持续增长,市场带来的挑战日益严峻。铁路零部件制造商需要利用此类测试系统来应对这一挑战,而测试团队需要利用这些测试系统在可控的试验室环境中对实现受电弓和接触网系统动态关系的精确仿真和模拟测试。产品设计人员可对运行环境中受电弓的响应有着更准确、更详细、更深入的了解,进而获得有意义的结论,开发出更高效、更可靠的受电弓系统。